As we all know, every product has its quality. LED lights are no exception, so what are the high-end LED lights? Now let’s seriously discuss this topic. I believe this is also a question that most people are curious about and desperately want to understand and discuss, and we all know that you get what you pay for, and we all know that there is no such thing as a good, cheap product, but people have in want to take advantage of the mind, and some businesses on the market will take advantage of this mind of consumers, selling fake and inferior products.
In life, everyone will play the role of a consumer and will use a variety of products, each product experience will be different, and even the same type of product will have good or bad quality. For example, anyone who’s ever used an iPhone will say that it’s good quality, it looks good, it’s ahead of the rest of the devices in terms of features, and it’s a great experience for consumers, only those who have used high-end products have such an experience.
If you have been using low-end products, you will only complain about the business this bad that bad, the manufacturer may be a lot of complaints, after-sales service will become more and more workload. Some products even changed several times are not good, this phenomenon, in the high-end products, brand products are rarely seen. So my advice is to be a rational consumer, don’t take any chances, blindly think you’ve got a good deal, it’s a superficial performance, this kind of business is not long-term.
For manufacturers, I think it is better to spend more time and money on improving the quality of production than to spend a lot of time dealing with these after-sales problems. If the manufacturer is producing the necessities of life, and the need for frequent replacement of products, the buy-back rate is not greatly increased?
What about the LED lights? I think everyone in life will be more or less in contact with the LED lights, then, you can be a good analysis of the products you use it? If you could, you’d be great. But I don’t think it’s possible to take up most of it?
So next I would like to share with you what is high-end LED lights?
If you are also a manufacturer or consumer of mid-to-high-end products, perhaps the following will help you.
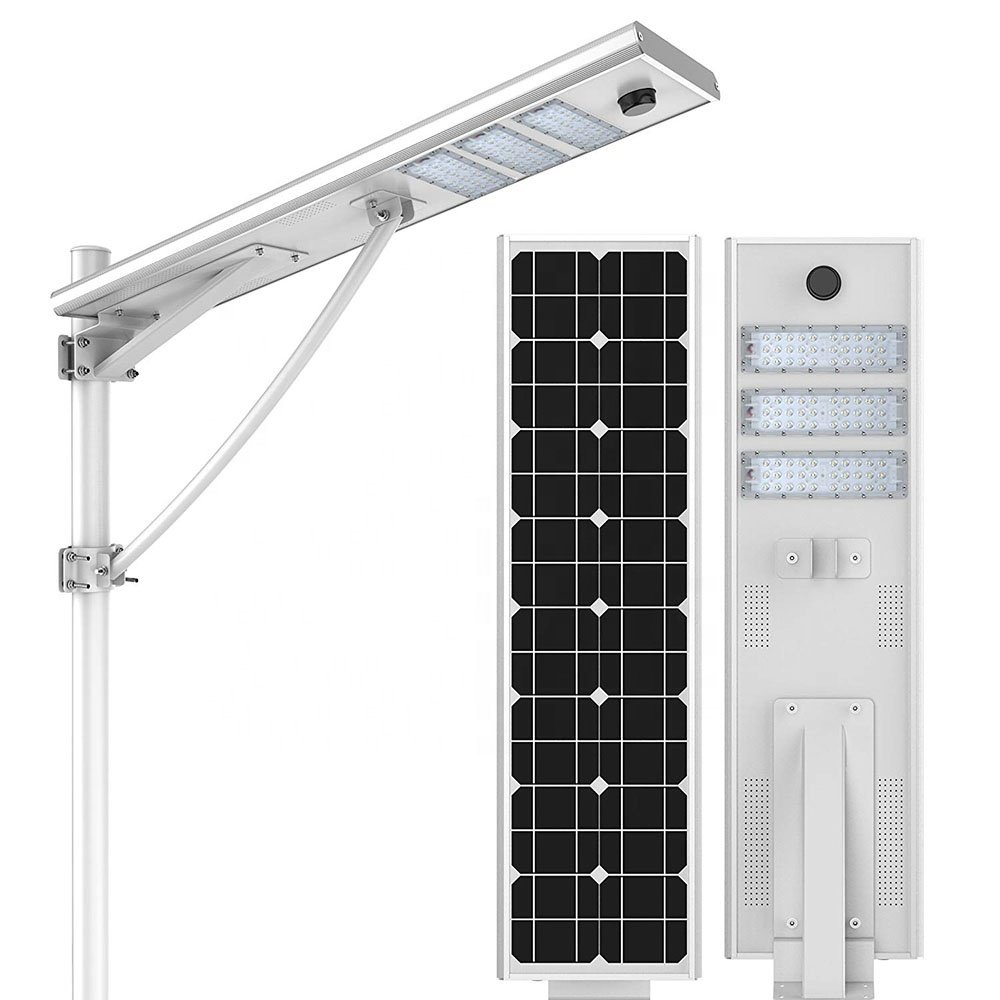
The basic structure of LED lights
The structure of an LED light mainly includes a frame, diffusion plate, light guide plate, light beads, driving power supply, aluminium substrate, and other components.
1, Frame: frame strength affects durability: the frame is an important part of the light, and the high strength of the frame makes the light more durable. LED light edge frame using different materials, its heat dissipation performance is not the same. According to statistics, the main frame of the light materials is aluminium alloy, steel, PC, A6063, aluminium-plastic, steel, and other materials.
2, Diffusion plate: different material transmittance is different: diffusion plate is the role of light guide plate to evenly diffuse but also plays the role of the fuzzy dot, the main materials used are acrylic, PC, PS, and so on. According to our understanding, the transmittance of acrylic is 92%, PC is 88%, PS is about 80%, the transmittance of acrylic material is higher than PC, the cost is lower, and its anti-ageing performance is weak; while the price of PC material is expensive, but the anti-ageing performance is strong.
3. Light guide plate: the plate has a significant influence on the light effect: the function of the light guide plate is to refract the light rays parallel to the direction of the light transmission plate to be perpendicular to the direction of the light transmission plate, and by the reflective paper will guide light plate refraction to the back of the flat light reflected out. In this process, but also to reduce light attenuation as far as possible, in general, the light efficiency of the light guide plate depends largely on the dot design, followed by the choice of plate.
4. Power supply: constant current power supply mode high efficiency: LED light has two kinds of driving power supply mode, one is constant current power supply, this mode high efficiency, PF value up to 0.95, cost-effective; the other is constant voltage with constant current power supply, stable performance, but low efficiency, high cost.
The above is LED light structure introduction, LED light with its good illumination uniformity, show the finger higher, light uniformity soft, comfortable and other characteristics, LED gradually become the best products of today’s era, LED lighting industry will be more and more space for development.
What material are the LED lights made of?
Led Light 5 big production materials: chip, bracket, silver glue, gold wire, epoxy.
(1) The chip
The composition of the chip: by the gold pad, P Pole, N Pole, PN junction, back gold layer composition (double pad chip without back gold layer). A wafer is a PN combination of player semiconductor elements and n-layer semiconductor elements rearranged by electron movement. This change enables the chip to be in a relatively stable state.
When a positive electrode is applied to the chip at a certain voltage, the holes in the forward p region will continuously swim toward the n region, and the electrons in the n region will move toward the p region relative to the holes. Like the electrons, the holes, move relative to each other, the holes pair up with each other, exciting photons and producing light energy.
Main classification, surface luminescence type: most of the light emitted from the surface of the chip. Five-side luminous type: surface, the side has more light-emitting according to the luminous color points, red, orange, yellow, yellow-green, pure green, standard green, blue-green, and blue.
(2) Stent
The structure of the bracket is 1 layer iron, 2 layer copper plating (good conductivity, heat dissipation), 3 layer nickel plating (anti-oxidation), 4 layer silver plating (good reflectivity, easy welding line)
(3) Silver colloid (for example, H20E)
Also known as white glue, it is opalescent in color, turns on adhesion (baking temperature: 100 â ° C 1.5 H), silver powder (conductive, heat-dissipating, wafer fixing) + epoxy (cured silver powder) + diluent (easy to stir).
(4) Gold wire (φ1.0 mil as an example)
The gold wire used in LED has φ1.0 mil, φ1.2 mil, the material of the gold wire, the material of gold wire used in LED is 99.9%, the use of gold wire
Using its high gold content, soft material, easy deformation, and good conductivity, good heat dissipation characteristics, the chip, and the stent form a closed circuit.
(E) Epoxy (e.g. EP 400)
Composition: A, B two groups of the agent.
Glue A: is the main agent, from Epoxy + defoamer + heat resistant agent + thinner.
B agent: is the curing agent, from the Acid Sound + release Agent + accelerator.
Package process
1. Led encapsulation task
The utility model connects an outer lead to an electrode of an LED chip, protects the LED chip at the same time, and plays the role of improving the light extraction efficiency. The key processes are mounting, pressure welding, and packaging.
2. LED package form
LED packaging can be said to be a variety of forms, mainly according to different applications using the corresponding size, heat countermeasures, and light effects. LED according to the packaging classification Light-LED, TOP-LED, Side-LED, SMD-LED, High-Power-LED, and so on.
3. LED packaging process flow
- Chip inspection
Microscopic examination: whether the material surface has mechanical damage and the pitting pit (Lockhill)
Whether the chip size and electrode size meet the process requirements
Whether the electrode pattern is complete
B) Expansion
Because the LED chip is still arranged closely after the slice spacing is very small (about 0.1 mm), not conducive to the operation of the post-process. We use a film expander on the bonding chip film expansion, which is LED chip spacing stretching to about 0.6 mm. Can also use manual expansion, but it is easy to cause chip drop waste and other undesirable problems.
C) Dispensing
Silver glue or insulating glue is applied at the corresponding position of the LED bracket. (for GaAs, SiC conductive substrate, red, yellow, yellow, and green chips with the back electrode, using silver glue. For blue and green led chips with sapphire insulating substrate, use insulating glue to fix the chip.)
The difficulty lies in the control of dispensing quantity. There are detailed process requirements in the colloid height and dispensing position.
As the storage and use of silver glue and insulating glue have strict requirements, the awakening of silver glue, mixing, and use time is a process that must pay attention to matters.
D) Preparation of adhesive
In contrast to dispensing, dispensing is using a dispenser to apply silver glue to the electrodes on the back of the LED, and then the lead with silver glue on the back is mounted on the led bracket. The efficiency of glue preparation is much higher than dispensing, but not all products are suitable for the glue preparation process.
E) Manual biopsy
The expanded LED chip (prepared glue or not) is arranged on the jig of the splinter stand, the LED bracket is placed under the jig, and the LED chip is punctured into the corresponding position one by one with a needle under the microscope. Compared with the automatic mount, the manual mount has the advantage that it is convenient to change different chips at any time. It is suitable for products that need to install many kinds of chips.
F) Automatic mounting
The automatic mounting is actually a combination of glue-dipping and chip-mounting two major steps, first in the led standpoint on silver glue (insulation glue), and then use a vacuum nozzle to suck up the LED chip moving position, and then arranged on the corresponding bracket position.
Automatic installation in the main process familiar with the equipment operation programming, while the equipment of the glue and installation accuracy adjustment. In the selection of the nozzle, the selection of Bakelite nozzle as far as possible to prevent damage to the LED chip surface, especially blue, and green chips must use Bakelite. Because the steel nozzle will scratch the chip surface of the current diffusion layer.
G) Sintered
Sintering aims to solidify silver colloids, and the sintering requires monitoring of temperature to prevent bad batch.
The sintering temperature of silver colloid is generally controlled at 150 ° C and the sintering time is 2 hours. The actual situation can be adjusted to 170 ° C, for 1 hour.
Insulation glue 150 ° C, 1 hour.
Silver Glue sintering oven must be under the process requirements of 2 hours (or 1 hour) to open the replacement of sinter products, the middle may not be opened at will. The sintering oven shall not be used for other purposes to prevent pollution.
H) Pressure welding
Pressure welding aims to lead the electrode to the LED chip to complete the connection of the lead wires inside and outside the product.
LED pressure welding process has gold wire ball welding and aluminium wire pressure welding two. The right picture is the aluminium wire pressure welding process, first on the LED chip electrode pressure on the first point, and then the aluminium wire pulled to the corresponding bracket above the pressure on the second point after breaking the aluminium wire. The process of gold wire ball welding is to burn a ball before pressing the first point, and the rest of the process is similar.
Pressure welding is a key link in LED packaging technology, the main need to monitor the process is pressure welding gold wire (aluminium wire) archwire shape, solder joint shape, and tension.
An in-depth study of the pressure welding process involves many problems, such as gold (aluminium) wire material, ultrasonic power, the pressure of pressure welding, selection of cutting tool (steel nozzle), movement track of cutting tool (steel nozzle), and so on. (below is a micrograph of the solder joint produced by two different splitters under the same conditions. The microstructure of the solder joint is different from that of the splitters, which affects the quality of the product.) We will not repeat it here.
I) Dispensing package
LED packaging is mainly a point of glue, potting, and moulding three. The difficulty of process control is a bubble, multi-material shortage, and black spot. Design is mainly on the selection of materials, the selection of a good combination of epoxy and stent. (general LED can not pass the air tightness test) as shown on the right top-LED and side-LED dispensing suitable packaging. Manual dispensing packages require a high level of operation (especially white LED), the main difficulty is controlling the amount of dispensing, because the epoxy will thicken during use. White LED dispensing also exists phosphor precipitate leads to the problem of light chromatic aberration.

J) Filling adhesive package
Light-led encapsulation is in the form of encapsulation. The process of encapsulation is to inject liquid epoxy into the cavity of the LED mould first, then insert the pressure-welded led bracket, put it into the oven to let the epoxy solidify, and then take the lead out of the mould cavity to form.
K) Molded package
Put the pressure-welded led bracket into the mould, close the upper and lower two sets of the mould with hydraulic press and vacuum, but the solid-state epoxy into the entrance of the injection duct and press the hydraulic ejector rod into the mould duct for heating, the epoxy enters each led moulding groove along the glue path and solidifies.
L) Curing and post-curing
Curing refers to the curing of epoxy packages, the general curing conditions of epoxy at 135 ° C, for 1 hour. The moulded package is typically at 150 ° C for 4 minutes.
M) After curing
Post-curing is to allows the epoxy fully cured, while the thermal ageing of the LED. Post-curing is very important to improve the bonding strength between epoxy and PCB. The general condition is 120 ° C for 4 hours.
N) cut tendon and slice
Because the LED lights are connected (not a single one) in production, Light-encapsulated LED lights cut the bars of the LED lights bracket. SMD-led is in a PCB board, the need for a scribing machine to complete the separation work.
O) Testing
Test the photoelectric parameters of LED, test the size of the shape, and at the same time according to customer requirements for LED product sorting.
P) Package
Count and package the finished product. Ultra-bright LED lights require antistatic packaging.
Select LED light methods
1, LED brightness is different, and the price is different. LED lights used in LED lights should be suitable for laser class I standards.
2, The anti-static ability of strong LED, long life, and therefore high price. Usually, antistatic larger than 700V LED can be used for LED lighting.
3, The wavelength of the same LED, color consistency, such as the requirements of color consistency, the price is high. It is difficult for manufacturers without LED spectrometers to produce products with pure color.
4, Leakage current LED is one-way conduction of light, if there is reverse current, called leakage, leakage current large LED, short life, low price.
5, Light-emitting angle use of different LED light-emitting angles is different. The price of a special luminous angle is higher.
6. The key to different quality of life is life, life is determined by light decay. Light decay small, long life, high price.
7, The light-emitting body of chip LED is a chip, different chip, and the price difference is very big. The chip of Japan, and the United States is more expensive, General Taiwan’s chip price is lower than Japan, the United States, the lowest home-made.
8、Colloid ordinary LED colloid is generally epoxy, with anti-UV and fire retardant LED prices are more expensive, high-quality outdoor LED lighting should be anti-UV and fire.
LED lights features
Advantages: LED intrinsic characteristics determine it is the ideal light source to replace the traditional light source, it has a wide range of uses.
1. Small size
LED lights are tiny chips that are encapsulated in epoxy, so they’re very small and very light.
2. Low power consumption
Led power consumption is very low, in general, LED operating voltage is 2-3.6 V. The operating current is 0.02-0.03 A. This means that it consumes no more than 0.1 W of electricity.
3. Long life
With the right current and voltage, LED lights can last up to 100,000 hours.
4. Be Green
LED lights are made of non-toxic materials, unlike fluorescent lights that can be contaminated with mercury, and LED lights can also be recycled.
5. Strong and durable
LED lights are completely encapsulated in epoxy and are stronger than bulbs and fluorescent tubes. There is no loose part of the light body, which makes the LED virtually indestructible.
In short, the middle and high-end products in the LED are to know more about their structure, and material, but also consider the use of the scene, environmental issues, durability issues, whether harmful to the body and a series of issues. For lights, I choose high-end LED lights. What do you think? If you feel that this article is helpful to you, or have any better suggestions or comments, feel free to leave us a message in the comments section, thank you.